Why Packout Testing is Crucial for Success
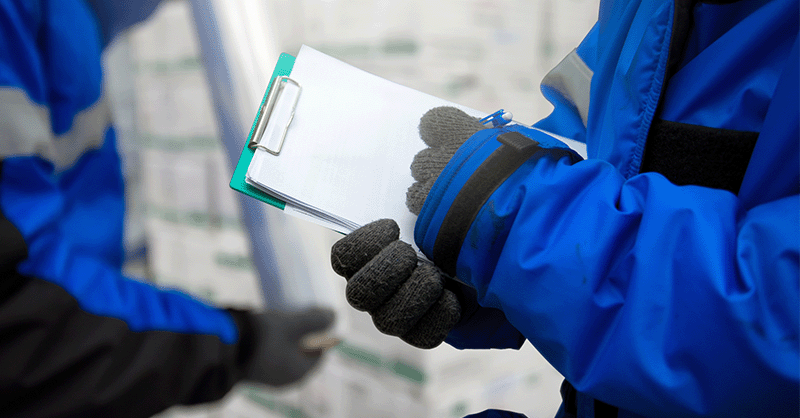
When pursuing a successful cool chain journey with high-value, temperature sensitive products, testing stands as a pivotal step. While testing might appear demanding and intricate, bypassing this phase could invite complexities that significantly affect your revenue and reputation.
Neglecting packaging testing can result in damaged and void product, jeopardizing both your bottom line and brand credibility, in a time where customer loyalty and trust can be difficult to secure. This remains true for anyone transporting product, but particularly for those with temperature sensitive product.
We've detailed below why you should be conducting testing on your cool chain pack-out and how to get started, to ensure your product moves swiftly into the hands of your customer, and in peak condition.
Importance of Testing
Testing allows you to understand the temperature sensitivity of your items, and what happens when they are exposed to undesirable temperatures and what those are. Your packaging and product's journey will be built from this, so to ensure time, revenue and reputation is not at risk.
You must test multiple configurations of cool chain materials to ensure they work to your product, it's ideal temperatures, and for however long or far you need as there is a high cost for untested packaging, that extends further than just damaged product.
What is at stake:
Your Revenue
When untested, product may become void during transit. This not only means that revenue lost on the product, and in replacing the product for the customer, but time, labour, freight, operational and packaging costs cannot be recouped. This, if continued, and on a wide scale, can impact a business's bottom line by a substantial amount if not corrected.
Customer Trust & Loyalty
When a customer receives damaged goods, or goods that aren't in peak condition, this breeds dissatisfaction, frustration, and if continued, can erode trust in your brand. The greatest cost of untested packaging, is the negative impact it can have on a customer's future buying patterns, and ultimately the loss of customer loyalty.
How to Test Effectively
As mentioned above, many are overwhelmed at the idea of testing. Not only do you need to know how to test, what temperatures to test at, and for how long, but additionally, how to interpret the data.
We suggest reading our How to Pack & Test Your Product blog to gain a better understanding of how to test your product specific to your product and it's journey in transit. A few points are noted below:
Test, test, test!
Test your chosen pack-out multiple times, and to multiple seasons, to ensure an average you are happy with.
Test for the worst case scenario
Could your package be delayed? Could it be left unattended at a customers home? Your testing should consider the longest possible time to the customer or their fridge, and still maintain your desired temperature.
Work with experts
Discuss your product journey with your courier company to determine your likely transit time. Work closely with your packaging supplier, as they may test your product with theirs for you, and share what product spec you need to reach your temperature requirements.
Still unsure? Talk to us.
We understand that testing is crucial but not easily done, and if done incorrectly the cost of lost business is significant.
This is why we offer testing of your product, with our packaging, to make sure we get it right the first time. We have in-house testing chambers, a dedicated team, and market-leading testing program, so get in touch!