Why Polybins Are Being Phased Out
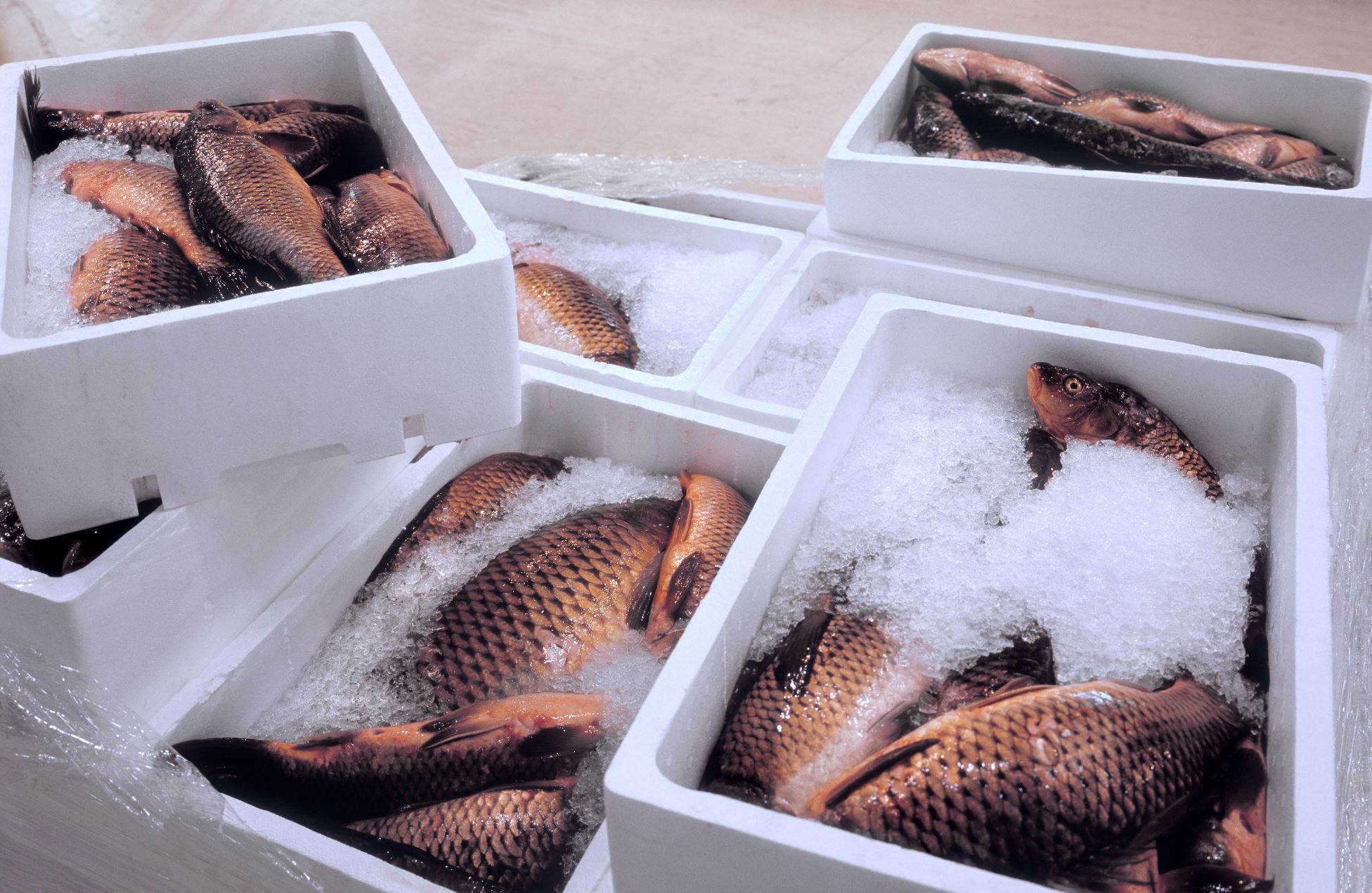
As the world seeks to diversify from its dependence on plastics and the wider petrochemical industry we are seeing legislative action taken from Governments around the world against products that are single use in nature or provide no meaningful recycling. One of those products is EPS or Expanded Polystyrene.
EPS was patented by the German chemical conglomerate BASF in 1951 and has since made it’s way into a number of industries as the packaging of choice for their cold chain requirements, All around the world, EPS is extremely prevalent in the pharmaceutical, seafood and vegetable and home delivery markets. Companies in these sectors have long argued that there is nothing comparable to EPS when it comes to its performance in thermal and structural characteristics. When you look at EPS from a packaging perspective it ticks a lot of boxes, it’s lightweight, stackable and comes palletised, can be made in a large volume format and is almost completely customisable. All of this means that for cold chain it’s almost ideal however EPS and it’s advantages are also it’s weaknesses. EPS is around 98% air which is what makes it such a good insulator.
The consequence of this means when you transport, store and send EPS you are using energy to move air – this is by default a grossly inefficient process and has a very direct effect on the environment. Even if we were to completely ignore the environmental impacts of producing EPS in the first-place efficiencies in the production, movement, storage and recovery of EPS means we have no option but to look outside of EPS and find a viable alternative. If you look at a very simple equation, a seafood business might use a 15 litre EPS box for their cold chain, you can fit between 60-70 complete EPS boxes on a pallet for this purpose, as a comparison you can fit around 200 RSC boxes on the same pallet and 800 insulation liners on the same pallet. Therefore, at an absolute minimum you have a 30% advantage on the inward component of using EPS, now the next major advantage is the outbound – there is NO kerbside recycling solution in Australia and many parts of the world for EPS, BASF have no facility, means or intention to recycle their product, end manufacturers of EPS provide a pickup service for their boxes however again the numbers become worrying, can only take EPS back in its form again moving 98% air. Cardboard by comparison be compacted into a pallet form and sent straight to a recycling centre to be re-purposed into new product. Then comes the insulation component – this is where EPS has always held an advantage however with a major NPD drive there are now multiple options that provide industry standard properties and are either fully kerbside recyclable, fully kerbside compostable or RedCycle recyclable.
The biggest hurdle to moving away from EPS has always been underlying thermal performance but now that is no longer a factor with alternatives and the unit cost is either cheaper or within range there is no excuse for companies not to at least investigate a more sustainable solution. Now that I have mentioned unit cost this is also incredibly important to note – once you factor in the overall savings from truck and warehouse fewer movements, fewer pallet movements, fewer labour hours, less power usage and less resources to produce the product the numbers start stacking up very quickly!
For EPS it’s advantages are also it’s weaknesses!